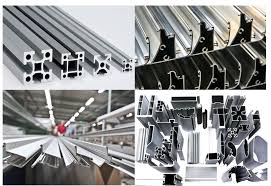
Aluminum fabrication plays a pivotal role in modern manufacturing, offering a blend of strength, versatility, and aesthetic appeal. This article delves into the intricacies of aluminum fabrication, highlighting its benefits, processes, and applications across various industries.
Understanding Aluminum Fabrication
Aluminum fabrication involves transforming raw aluminum into finished products through processes like cutting, bending, welding, and assembling. Its lightweight nature, corrosion resistance, and malleability make it a preferred choice for many applications.
Advantages of Aluminum Fabrication
1. Lightweight and Strong
Aluminum offers a high strength-to-weight ratio, making it ideal for applications where weight reduction is crucial without compromising structural integrity.
2. Corrosion Resistance
Naturally forming a protective oxide layer, aluminum resists corrosion, ensuring longevity even in harsh environments.
3. Versatility in Design
Aluminum can be easily machined, cast, or extruded into complex shapes, allowing for innovative and customized designs.
4. Recyclability
Being 100% recyclable without loss of properties, aluminum supports sustainable manufacturing practices.
Customization in Aluminum Fabrication
Custom aluminum fabrication tailors products to specific requirements, enhancing functionality and aesthetics. This customization is vital in industries like aerospace, automotive, and architecture, where precision and performance are paramount.
Applications Across Industries
Aerospace
Aluminum’s lightweight and strength make it indispensable in aircraft structures, contributing to fuel efficiency and performance.
Automotive
Used in frames, panels, and engine components, aluminum helps in reducing vehicle weight, enhancing speed, and improving fuel economy.
Construction
From window frames to structural components, aluminum’s durability and aesthetic appeal make it a staple in modern architecture.
Electronics
Aluminum’s excellent thermal conductivity makes it ideal for heat sinks and other electronic components.
Choosing the Right Fabrication Partner
When selecting an aluminum fabrication service, consider:
Experience and Expertise: Ensure the provider has a proven track record in delivering quality products.
Customization Capabilities: Ability to tailor solutions to specific needs.
Quality Assurance: Adherence to industry standards and certifications.
Technological Advancements: Utilization of modern equipment and techniques for precision and efficiency.
Conclusion
Aluminum fabrication stands at the forefront of modern manufacturing, offering unmatched benefits in durability, design flexibility, and sustainability. By leveraging expert fabrication services, businesses can achieve customized solutions that meet their specific needs, ensuring quality and performance across various applications
Article No: 16
Your Go-To Guide for High-Quality Aluminum Fabrication Solutions
In the world of modern manufacturing and construction, aluminum stands out as one of the most versatile and widely used metals. From aerospace components and automotive parts to architectural structures and consumer products, aluminum’s strength-to-weight ratio, resistance to corrosion, and adaptability to various fabrication methods make it an essential material.
This comprehensive guide will walk you through everything you need to know about aluminum fabrication — from the basics and benefits to the fabrication techniques, applications, and how to choose the right fabrication partner.
What is Aluminum Fabrication?
Aluminum fabrication is the process of creating structures and products from aluminum using various techniques such as cutting, bending, welding, machining, and assembling. Unlike raw aluminum that is mined and processed into sheets or bars, aluminum fabrication is the art and science of turning these materials into finished or semi-finished products according to specific designs and needs.
Aluminum fabrication encompasses a wide range of services including:
Custom aluminum sheet metal work
CNC machining of aluminum parts
Extrusion-based fabrication
Aluminum welding
Powder coating and anodizing
Assembly of aluminum components
Whether you’re developing a prototype, constructing a building, or producing high-performance equipment, aluminum fabrication offers the flexibility and durability required to bring complex ideas to life.
Why Choose Aluminum?
Before diving into the fabrication processes, it’s important to understand why aluminum is a preferred material for so many industries. Here are the core advantages:
1. Lightweight Yet Strong
Aluminum is about one-third the weight of steel, which makes it ideal for applications where weight matters — such as aerospace, automotive, and even portable consumer products. Despite its light weight, aluminum can be alloyed and heat-treated to achieve impressive strength.
2. Corrosion Resistance
Aluminum naturally forms a protective oxide coating that resists rust and corrosion, even in marine and industrial environments. This property greatly reduces the need for regular maintenance.
3. High Thermal and Electrical Conductivity
Aluminum is an excellent conductor of heat and electricity, which is why it’s used extensively in electrical transmission lines, heat exchangers, and computer cooling systems.
4. Recyclability
Aluminum is 100% recyclable without loss of properties, making it one of the most sustainable metals available. Recycling aluminum uses only 5% of the energy required to produce it from ore.
5. Aesthetic Flexibility
Aluminum can be anodized, polished, brushed, or powder coated in a range of colors and finishes, making it both functional and visually appealing.
Key Aluminum Fabrication Techniques
1. Cutting
Aluminum is typically cut using laser, water jet, or plasma cutting systems. These tools provide high precision and speed, especially for complex geometries. Shearing and sawing are also used for simpler cuts.
2. Forming and Bending
Forming aluminum involves applying mechanical force to shape the material without removing any part of it. Techniques include press braking, roll forming, and stamping. Since aluminum is softer than steel, it requires careful handling to avoid warping or cracking.
3. Welding
Aluminum can be challenging to weld due to its thermal conductivity and oxide layer. However, with the right techniques — such as TIG (Tungsten Inert Gas) and MIG (Metal Inert Gas) welding — fabricators can achieve strong, clean welds.
4. Machining
CNC (Computer Numerical Control) machines are used to precisely remove material from aluminum workpieces. Drilling, turning, milling, and tapping are common machining processes.
5. Finishing
Surface finishing enhances both the appearance and durability of fabricated aluminum parts. Popular methods include:
Anodizing – for corrosion resistance and decorative effects
Powder coating – for color and protection
Polishing and brushing – for sleek, modern aesthetics
Types of Aluminum Used in Fabrication
Different aluminum grades are suited for different types of fabrication. Here are a few commonly used alloys:
6061 Aluminum: Known for its strength, weldability, and machinability. Ideal for structural applications.
5052 Aluminum: Highly resistant to corrosion and commonly used in marine environments.
2024 Aluminum: High strength and fatigue resistance, often used in aerospace.
7075 Aluminum: Extremely strong and used in high-performance gear, but harder to weld or form.
Understanding the material properties is essential in choosing the right alloy for your application.
Applications of Aluminum Fabrication
The possibilities with aluminum fabrication are virtually endless. Here’s a look at how various industries rely on aluminum solutions:
1. Architecture and Construction
From window frames and curtain walls to railings and roofing panels, aluminum provides the strength, durability, and visual appeal needed in modern building design.
2. Transportation
Aluminum is a key material in cars, airplanes, and trains. It helps reduce weight, improve fuel efficiency, and increase overall performance. Aircraft structures, wheels, engine components, and panels are just a few examples.
3. Electronics
Because aluminum dissipates heat efficiently, it’s widely used in electronic housings, cooling fins, and LED lighting fixtures.
4. Consumer Goods
From smartphones and laptops to furniture and sports equipment, aluminum is used to make lightweight, stylish, and durable products.
5. Industrial Equipment
Aluminum fabrication supports the production of conveyor systems, platforms, enclosures, and tools used in factories and warehouses.
Custom Aluminum Fabrication: Tailoring to Your Needs
Off-the-shelf parts often can’t meet the specific requirements of complex projects. That’s where custom aluminum fabrication comes in.
A good fabrication shop will work closely with your design team to produce one-of-a-kind or limited-run components with exact dimensions, finishes, and functionalities. This process may involve prototyping, CAD modeling, and multiple fabrication methods to ensure perfection.
Benefits of custom fabrication:
Tailored dimensions and features
Reduced material waste
Increased performance and efficiency
Unique branding or design possibilities
Factors to Consider When Choosing a Fabrication Partner
Choosing the right aluminum fabrication company is crucial for quality, efficiency, and cost-effectiveness. Here’s what to look for:
1. Experience and Expertise
A company with years of experience in aluminum fabrication will understand the nuances of the material and be equipped to handle both simple and complex projects.
2. Capabilities and Equipment
Does the shop have the necessary tools like CNC machines, press brakes, welding bays, and finishing stations? A modern facility ensures faster turnaround and consistent quality.
3. Design Support
A strong in-house design and engineering team can optimize your project for manufacturing and cost-efficiency. Look for providers that offer CAD/CAM services and prototyping.
4. Certifications and Standards
Ensure the company adheres to quality management systems like ISO 9001 and holds any industry-specific certifications (e.g., AWS for welding).
5. Reputation and Reviews
Check client testimonials, case studies, and online reviews to get a sense of the company’s reliability and customer satisfaction.
6. Turnaround Time and Flexibility
Speed and adaptability are essential in today’s fast-paced world. A good partner should meet deadlines and accommodate design changes when necessary.
Cost Considerations in Aluminum Fabrication
Several factors influence the cost of aluminum fabrication:
Material Grade: Premium alloys like 7075 cost more than standard grades.
Complexity of Design: Intricate shapes, tight tolerances, and custom finishes increase costs.
Volume: Bulk orders reduce the cost per unit, while one-off custom parts are more expensive.
Finishing Requirements: Anodizing, powder coating, or polishing adds to labor and materials.
Tooling and Setup: Custom tools, jigs, and dies are needed for specialized parts, which can affect the initial project cost.
Working closely with your fabricator during the planning phase helps optimize cost without compromising quality.
Trends in Aluminum Fabrication
The field of aluminum fabrication is constantly evolving with advancements in technology. Here are some trends shaping the industry:
1. Automation and Robotics
CNC automation and robotic welding are improving precision, repeatability, and production speed.
2. 3D Printing and Additive Manufacturing
While still in its early stages with metals, aluminum 3D printing is opening doors to new possibilities in prototyping and lightweight structures.
3. Sustainable Fabrication
With a push toward green manufacturing, more shops are adopting energy-efficient practices and maximizing recycling of aluminum scraps.
4. Digital Twin Technology
Digital modeling of the fabrication process — or “digital twinning” — allows manufacturers to simulate and refine the process before production begins.
Final Thoughts
Aluminum fabrication is a cornerstone of modern manufacturing, powering everything from our buildings and vehicles to the gadgets we use every day. Its unique combination of strength, lightness, corrosion resistance, and adaptability makes it a dream material for designers and engineers alike.
Whether you’re looking for a one-time custom build or a long-term fabrication partner, understanding the essentials of aluminum fabrication will help you make smarter decisions, avoid costly mistakes, and bring your ideas to life with confidence.